We have established three production plants in the Tokyo metropolitan area and responsed to all customer needs quickly.
Sagamihara Plant
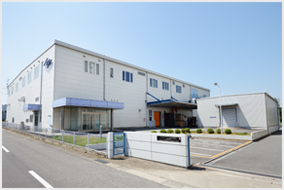
1787-1 Negoya, Midori-ku, Sagamihara-Shi, Kanagawa, Japan
Site area: 661 square meters
1F: 23 injection molding machines (100t ~ 280t), 23 automatic take-out machines, production office, mold maintenance room, workshop, carton material storage
2F: material mixing chamber
3F: 5 assembly lines, 2 belt inspection lines, general affairs office, drawing room, conference room, quality control room, development office
Outbuilding: automated warehouse, material warehouse.
Ibaraki Plant
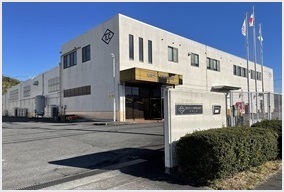
644-34, Hitana, Nakagouchou, Kitaibaraki-Shi, Ibaraki, Japan
Site area: 13,223 square meters
1F: 20 injection molding machines (180t ~ 280t), 20 automatic take-out machines, 10 assembly lines, belt inspection lines, production office, sub-material yard, workshop, mold maintenance room
:1.5F: material mixing room
2F: general affairs office, meeting room, drawing room, quality control room, development office
Outbuilding: assembly plant (Plant No. 2), 5 material warehouses
Tokyo Plant
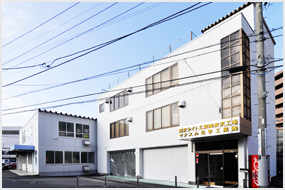
4-8-32 Nishihashimoto, Midori-ku, Sagamihara-Shi, Kanagawa, Japan
Site area: 1,322 square meters
1F: injection molding machine (7t,50t), material storage, production office
2F: belt inspection line, 4 hot stamp machines, shrink machine, quality control room
3F: office, reception conference room